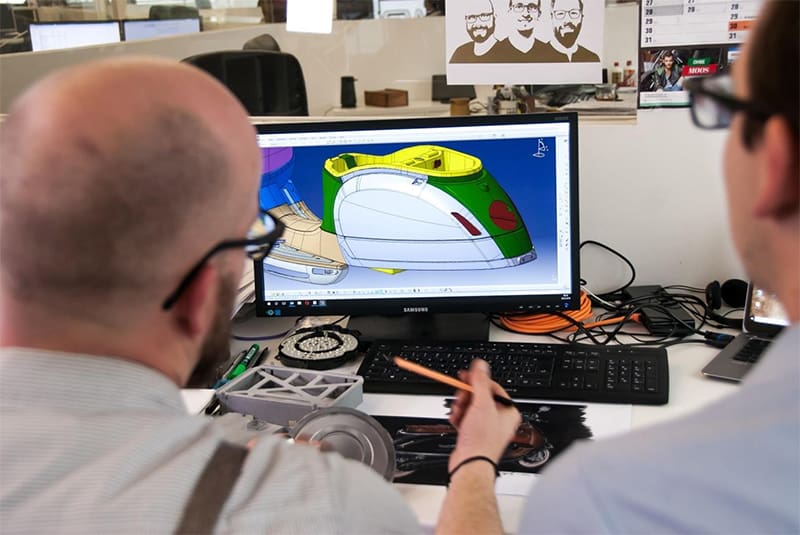
Computational fluid dynamics or CFD involves the analysis of fluid flow, heat transfer, and associated systems with the help of computer-based simulation. It has a wide range of industrial and non-industrial applications and is a very robust tool for product manufacturing. It is excessively used in automobile industries for predicting drag forces and lift of the vehicle. Computational fluid dynamics requires significant knowledge in fluid dynamics, mathematics, and programming. It involves assuming the wide-ranging of variables to generate models that can capture the required needs for the actual real-world system.
Computational fluid dynamics technique is utilized for the study of aircraft and vehicle. It is helpful in analyzing the lift and drag of the vehicle. The hydrodynamics of ships can be easily examined with this method. The study of combustion in internal combustion engines and gas turbines in industrial power plants and the flow inside rotating passages and diffusers in turbomachinery can be easily done with the use of this technique. In biomedical engineering, it is employed for blood flow analysis through veins and arteries. It is also used for weather prediction by the meteorology department. Modern environmentalists are also using this technique for determining the distribution of effluents and pollutants.
Industrial units are in awe with the computational fluid dynamics as it offers unique advantages over the experiment based techniques to fluid or flow systems design. It allows unlimited levels of details of results and helps to perfect the fluid systems. It reduces the lead times and costs of new designs for a system substantially. CFD facilitates analysis of the system where controlled systems are difficult to perform. It also has the ability to examine systems under disastrous conditions at and beyond their normal performance units. In experimentation studies, the costs of hiring personal and other aspects are variable and hence experimentation is increasingly being ignored by the industries. On the other hand, computational fluid dynamics deliver a huge volume of results without any added cost and is very cheap to perform.
Fluid flow problems can be tackled by computational fluid dynamics codes. These codes are structured around the numerical algorithms and allow smooth access to solve difficult fluid flow problems. A computational fluid dynamic codes consist of a pre-processor, a solver, a post-processor.
The input of a fluid problem to a CFD program for transformation into an easy part comes into the context of pre-processing. It basically involves defining the geometry of a particular region, ie. a computational domain. It is further divided into a number of smaller, non- overlapping sub-domains in the form of mesh or grid of cells that helps in grid generation. It helps in defining and modeling of fluid properties of a fluid. The solution to such variables such as temperature, pressure, etc. is defined at nodes at each grid. The accuracy of any CFD solution is governed by the number of cells in the grid as the greater the number of cells or grids, the greater the solution accuracy. The fineness of the grid depends on the cost of the system and the accuracy of a solution. Most of the time of any computational fluid dynamics project is utilized at grid generation and domain geometry.
The finite difference, finite element, and spectral methods are three basic numerical solution techniques out of which the finite difference method is mostly used. A numerical algorithm involves integrating the basic equations of fluid flow over all the finite volumes of the region. The resulting integral equations are then transformed into a system of algebraic equations. The algebraic equations are then solved by an iterative method. The basic difference between the finite volume method and other CFD techniques is the integration of the control volume in the finite volume method. The resulting equations have the same properties for each finite-size cell. This simple concept makes it easy for engineers to understand the fluid flow as compared to other methods. The conservation of various flow variables such as enthalpy, velocity within a finite control volume is expressed to estimate whether it increases or decreases. Computational fluid dynamics codes consist of discretization techniques that are helpful for convection, diffusion, and other key transport phenomena.
The ever increasing popularity of CFD software has extended the processing capabilities. It has facilitated great graphic capabilities along with domain geometry, and grid display. The software package of CFD now includes vector plots, line and shaded contour plots, contour postscript output, and particle tracking. These facilities are enhanced by the animated and dynamic result display. This has allowed transmission of ideas to people of non-engineering backgrounds.
The fluid flow problems are built on complex sets of physics, chemistry, mathematics concepts, and mastering them requires skillful professionals. The user must possess significant knowledge in the various subjects prior to the simulation of CFD problems. The user must be able to identify and formulate the chemical and physical aspects of the flow problem. The key decisions that go with the modeling of fluid flow are the effects of ambient temperature, variations in air density, turbulent flow, and air bubbles, etc. The right decisions should be made while modeling the equations as to preserve the necessary characteristics of the problem. The accuracy at the simplification of the equation allows the greater quality of the CFD. The detailed description of the domain geometry and grid design is crucial at the initial stage for obtaining successful simulation results. Successful simulations can be obtained by convergence and grid dependence. A converged solution can be achieved by selecting various acceleration devices and relaxation factors.
The converged solutions are filled with varied issues and require optimization. The optimization of the solution with speed needs extensive experience at the evaluation of the code. The initial grid design depends on the characteristics of the flow. It is filled with numerous errors and requires refinement. Errors can be eliminated by performing a grid dependence study. Each algorithm has a unique error pattern and can be guessed by an experienced professional who has a thorough knowledge of the algorithm.
Computational Fluid Dynamics (CFD) is a way of reorganizing such processes and systems in a series of differential equations by using digital computers. It offers qualitative and quantitative reasoning of fluid flows by the use of mathematical modeling, discretization, and other pre- and post-processing tools. It has helped the scientists enormously in the development of fluid dynamics. It has replaced the traditional approaches to fluid dynamics with more powerful computational tools. The results of the computational fluid dynamics are equivalent to the actual laboratory results.
The ultimate goal of growth in the CFD field is to offer a capability comparable with other CAE applications such as stress analysis codes. The key reason why CFD has remained behind is the significant complexity of the existing behavior, which precludes a description of fluid flows that are simultaneously economical and complete.
The availability of affordable high-performance computing hardware and the introduction of user-friendly interfaces have led to a recent upsurge of interest, and CFD has entered into the wider industrial community. The variable expense of an experiment, in terms of facility hire and/or person-hour costs, is directly proportional to the number of data points and configurations tested. Whereas CFD codes can generate extremely large volumes of solutions at no added expense. It is very cheap and easy to perform parametric studies such as optimizing equipment performance.
The accuracy of a Computational fluid dynamics solution is determined by the number of cells in the grid. Generally, larger the number of cells, the better the solution accuracy. Both the accuracy of a solution and its cost in terms of necessary computer hardware and calculation time is dependent on the fineness of the grid. Optimal meshes are often varied, finer in places where greater variations occur from point to point and coarser in regions with relatively less difference.
Efforts are underway to generate CFD codes with a self-adaptive meshing ability. Ultimately such programs will itself refine the grid in regions of rapid variations. A significant amount of basic development work still needs to be done before these programs are robust enough to be incorporated into industrial CFD codes. The main ingredients for success in CFD are experience and a thorough understanding of the physics of fluid flows and the fundamentals of the numerical algorithms. Without these, it is very unlikely that the user will get the best out of code. It is the intention of this book to provide all the necessary background material for a good understanding of the internal workings of a CFD code and its successful operation.
Also Read: Applications Of Computational Fluid Dynamics