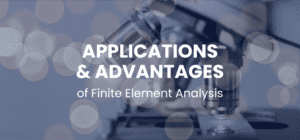
Finite Element Analysis, often known as the “Finite Element Method,” is a systematic technique for solving differential equations numerically in engineering and mathematical modeling. It is a recommended way to predict how an assembly will act in a certain situation.
This method is popular in many technical fields because it provides exact solutions to common problems of relevance. FEA entails the breakdown of an issue into micro-problems in order to arrive at a solution. So, this blog is to gauge its micro applications and advantages.
What is Finite Element Analysis?
Finite Element Analysis (FEA) is a computer technique that predicts how goods and materials will react to forces and other physical factors such as vibrations, heat, and fluid flow in the actual world. This is essential since it indicates whether a product will succeed or fail.
If a product cannot withstand the conditions under which it must work, it must be reevaluated; the advantage of employing finite element analysis at this point is that the product has not yet been manufactured.
Principles of the Finite Element Method
The principles underlying finite element analysis include boundary conditions, such as forces and pressures, and three governing equations:
- Equations of equilibrium that determine when opposing forces or effects are balanced.
- Strain-displacement relations, quantify the deformation a structure undergoes in response to a specific set of external shocks.
- The behavior of a metal or substance to external stimuli can be predicted by constitutive equations, which are relations between two physical parameters that are unique to the material.
Types of Finite Element Analysis tests
During finite element analysis, a variety of tests are utilized, including
- Static structural analysis:
This method of FEA analyzes a proportionally sized model. Any structure that is sound on a small scale will be able to manage the same interactions as the full-size structure and generate the same results, according to the test.
- Analysis of thermal engineering techniques:
Thermal analysis refers to the diversity of techniques developed and employed to constantly measure any physical property of a product or system as a function of temperature. While operating, electronic circuits, engines, and machines all generate heat.
- Modal analysis:
Everything vibrates at a certain frequency, so it is essential to do a modal analysis to determine how disruptive external vibrations affect the structure of the product. This type of finite element analysis also enables users to account for vibrations during the design phase, resulting in a durable end product.
- Seismic engineering calculations:
This test enables designers to comprehend the product’s response to varying ground frequencies and vibrations, ensuring a solid foundation for the final structure.
Advantages of Finite Element Analysis
- Finite element analysis offers the safe simulation of potentially dangerous or destructive load circumstances and failure modes, allowing engineers to find a system’s physical reaction at any place. Other benefits include
- Increased accuracy due to the study of any physical stress that can damage the design.
- Because designers may witness how stresses within one piece can affect the materials of a related element, the design is enhanced.
- Earlier testing in the development process. Virtual prototyping enables the designer to simulate different designs and materials in a matter of hours, as opposed to the days required to create physical prototypes.
- Increased productivity and income as a result of the fact that FEA software enables designers to manufacture higher quality products in a faster design cycle with less material usage.
- Enhanced insight into important design parameters as the result of being able to simulate both the design’s interior and the exterior. This permits designers to evaluate how essential components influence the structure as a whole, as well as why and where failures may occur.
- Optimal utilization of models because a single model can be used to simulate several failure modes or physical events.
- Quick computation times and reasonable investment expenses.
- Access to existing experimental results, which can be retrieved from the parametric analyses of already validated models and used in the new model.
Applications of Finite Element Method
FEA has multiple applications, among which a few are noted below.
- Stress Analysis– Stress, strain, failure points, fatigue, creep.
- Thermal Analysis– Conduction, convection, radiation, conjugate heat transfer.
- Vibration Analysis– Modal, harmonic, random, transient dynamic.
- Seismic Analysis– Equivalent static, response spectrum, transient dynamics.
- Impact & Crash Analysis– Equivalent static, short duration explicit simulation.
Wrapping Up
Finite Element Analysis is considered in the pre-product development stage to gauge its features and the optimizations required. FEA can be used as a “standalone option” or as part of a suite of analytical choices during the design process to develop and evaluate a product.
Technosoft Engineering offers premier structural stress analysis, pipe stress analysis, and finite element analysis (FEA) services, ensuring structural and functional integrity for safe and optimal system design.
With over a decade of engineering experience, we are able to assist clients in resolving their most difficult technical, design, and engineering issues, as well as deliver competitive and cost-effective solutions for optimizing the design of structures.