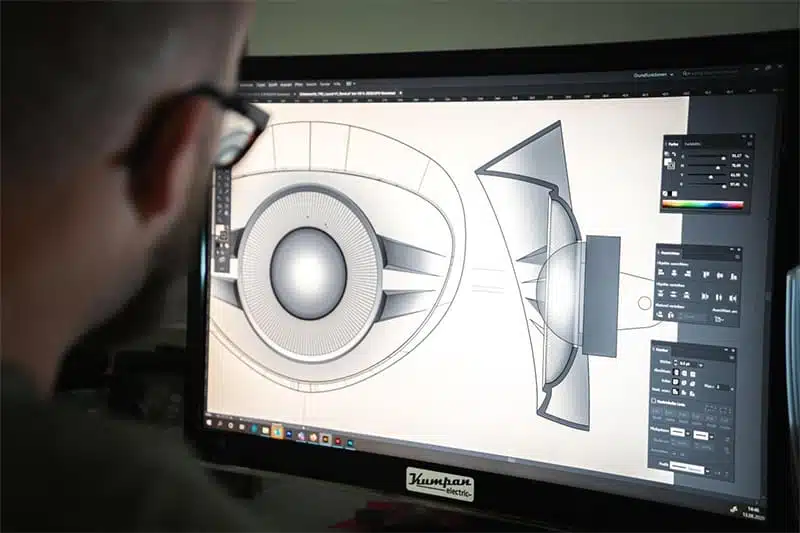
Computational Fluid Dynamics (CFD) is a way of rearranging such processes and systems in a series of differentiating statistics using digital computers. It provides appropriate consultation with the amount of fluid flow through mathematical modeling, optional, and other pre-and post-processing tools. It has greatly helped scientists to improve the strength of the liquid. It has replaced traditional liquid energy methods with more powerful computational tools. The potential effects of computational fluid are comparable to actual laboratory results. Computational Fluid Dynamics is based on the basic physiological mechanisms of the following fluid forces:
- Energy Conservation
- Newton’s second law
- Mass Conservation
The result of CFD is usually a set of numbers for the purpose of engineering analysis. Most of the powerful Computational fluid dynamics numerical algorithms we use today are deeply embedded in the mathematical structures of flow equations. It empowers designers and designers to design safe and comfortable environments. It enhances the aerodynamic features of the aircraft by influencing small details. It is also used to reduce health risks from radiation and other hazards. This technology is increasingly being used to simulate walking on a car. Estimates of the pressure field influenced by the rotor by helicopter fuselage can be estimated with the help of this technology. Biomedical engineering has been widely used in circulatory and respiratory systems. The impact of this technology is growing rapidly as it is less expensive. But modern flow measurement is complex and flawed and therefore requires a lot of engineering expertise to approach the desired solutions.
CFD Services uses well-designed geometry and has an understanding of the expected imitation effects that aids the process of obtaining a successful analysis. With special care in modeling and setting your imitation at the beginning of the analysis process, you are likely to save a lot of time over time. Before you can use simulation, and trust the results of the simulation, you must have an accurate measurement and description of the results. These estimates may be based on previous experience or based on previous models or industry performance. Having an idea of what the results should allow you to “mentally test” the effects of simulation. This is important because the performance of CFD results depends on the user’s valid input into the software. If you see unexpected results, you can easily spot potential errors in the simulation settings.
To create a CAD model that is very useful in your CFD analysis, it is important that you first know that you are interested in modeling internal or external flow. In the internal flow bound to solid objects such as pipes, you can simply model a standard object in 3D CAD software. If the flow is around a non-physical object, you can re-enter the model in simulation CFD. In the meantime, you will build a bounding box around the object that describes the size of the liquid flowing around the object. Alternatively, you can create a space around the object firmly inside your CAD software; usually by making a large box around the real thing like a new body. You can then import these bodies into Simulation CFD and set the external ones as any solvent fluid and solids in any structures it needs. This may be necessary if you are not able to adjust the size of the bounding box using the methods designed for Simulation CFD.
For a good CFD analysis, the model needs to be given enough details to show the truth, but not so much detail that it takes less time to do. Water flow can be very sensitive to small details and in addition to simplifying the model, one can miss some of that detail. However, simplification will result in the meshes taking too long to work without increasing the accuracy of the results. Therefore, it is important to leave those details that will not affect the flow, while including that information that will affect the flow. As with FEA, the first step in CFD meshing is usually with software to create automated machine distribution. This mesh is usually a course in places and maybe good for others as well. Mesh refining in CFD is exactly the same as FEA and can be treated in the same way by using built-in filter tools.
A very rough mesh will not be accurate enough to produce the right imitation results. Such a machine often creates dramatic results or displays some of the clearest artistic indications that something is wrong. A very good mesh requires a lot of computing power that can prevent it from performing analysis, or rediscovering the right design solution. One solution is known as adapting meshing, which filters the mesh according to the repetitive effects of the simulation. By using simulation many times, this tool only filters certain areas of the match to meet the correct solution. Here, we should note the differences between the mesh junction and the solution junction, which are discussed further in the resolution phase. For the flexible meshing to be more efficient, care must be taken to create a good first mesh.
During the geometry phase, the CFD engineer prepares the CAD Geometry for the CFD solution, which requires a solid 3D volume of its geometry. CFD requires very high standards in geometric quality than the average person. First, an engineer refines CAD geometry. They redefine areas with simple geometry, removing unnecessary elements such as ties and small details. They search for spaces and holes and often clean up a host of problems that cause problems in a CFD solution. The quality of the CFD machine is built from the quality of the original CAD geometry. Limitations on negative geometry restrict the predictive quality of low CFD. After introducing geometry into CFD software, the engineer created a CFD model. This incorporates physics into geometry. CFD simulations do not automatically load all the physics in the world; computer load can exceed most computers. Instead, the engineer selects the appropriate physics models, the parameters of the input model, and usually incorporates the required physics into your CFD simulation.
The mesh divides the geometry into millions of tiny cells. The combination of these cells and structured physics allows the software to solve the CFD problem. But not all meshes are made equal. Hinges of imitation quality in finding the right size of these cells in the right place. Mesh measurement is a key way to control a CFD engineer; they focus most of their time on this step. Requires a repetitive process: try certain match settings; check imitation; check results; improve match settings. There is no effective simulation for the first time. The engineer is looking at a number of potential problems:
- Incorrect physics settings
- Problem areas that require additional match fixes
- Imitating instability
- Bad results
- Some unknown problems.
The independent mesh study systematically evaluates imitations of various sizes and compares simulation results with each mesh size. The engineer searches for an independent mesh state where the results do not change with the size of the match. Once achieved, the engineer can predict the accuracy of the simulation. The next step specifies numerical parameters, e.g. to set solver parameters, discretization schemes, etc. Depending on the type of simulation, each problem has its own unique structure. Usually, one problem can be solved with repetitive solutions and different solver parameters; however, to solve the problem successfully, it is very important to provide appropriate solver parameters and number systems.
The green output from the CFD simulation is a database of numerical data, which can be easily interpreted by humans. In post-processing, an engineer converts that database into a variety of presentations, highlighting key points. These are usually visual images. But they can also be tables, prices somewhere, or just about any other type of data requested. Discuss the results with your engineer before starting production. Developer programs for most of these output files in one template before making multiple copies in each simulation situation. Generally, engineers are happy to add additional posts to the template. More work comes from adding post usage after the fact because they need to manually edit the processing of each post in each simulation file.
Finally, the engineer writes everything in the report. In addition to the results, the report should provide sufficient detail for the third party to produce a CFD simulation. This serves as an alternative to quality control. Many companies strike a balance between reporting excessive information and protecting their technology. Usually, they will happily explain the simulation settings, but capture details about the exact size of the match. This is because most of the imitation quality is based on mesh size.
Also Read: Role Of Computational Fluid Dynamics In Product Manufacturing